Using an overhead conveyor in your distribution center
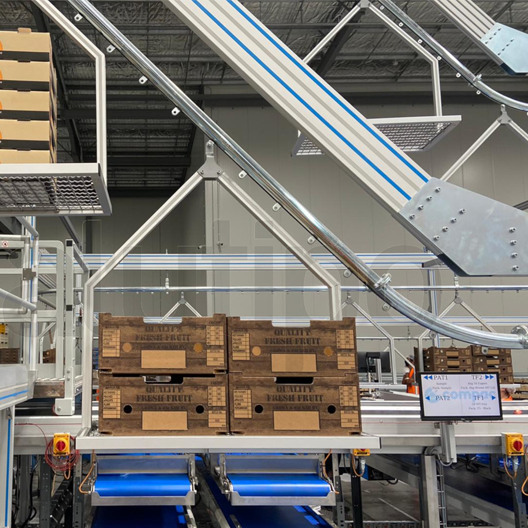
Why use an overhead conveyor (monorail) in your distribution center or warehouse operations?
In distribution centers and warehouses, where space optimization and streamlined processes are essential for maximum efficiency and productivity, traditional methods of moving empty boxes and containers can sometimes struggle to meet the dynamic needs of the environment. Air conveyor systems, often referred to as monorails, provide an effective solution to these challenges. They literally elevate the process, utilizing often underutilized overhead space. Below is a list of seven advantages that overhead monorails bring to distribution center and warehouse operations.
1. Occupies unused overhead space and frees up floor space.
One of the most important advantages of integrating an overhead monorail system is its ability to utilize overhead space that is often overlooked. Unlike other methods of delivering and removing boxes that consume valuable space, overhead monorails free up land for more critical operations. This not only improves the flow of movement within the facility, but also improves safety by reducing clutter and potential tripping hazards.
2. Centralized corrugated cardboard storage and loading of empty boxes
Efficiency in distribution centers depends to a large extent on streamlined material handling. Overhead conveyors facilitate the centralized storage of corrugated cardboard, simplifying the process of loading empty cartons. This centralization minimizes the time and labor required to manage these materials, leading to more efficient operations.
3. Allows delivery of empty boxes at an ergonomic height.
Ergonomics play a key role in maintaining a productive and healthy workforce. Overhead conveyors are designed to deliver boxes at an ergonomic height, minimizing the need for excessive bending or stretching. This improves worker comfort and significantly reduces the risk of injury, contributing to a happier and more efficient workforce.
4. Custom-designed carriers to maximize delivery rates.
Each distribution center has unique needs based on the size and type of cases it handles. Pacline offers custom designed conveyors to maximize delivery rates for specific case sizes.

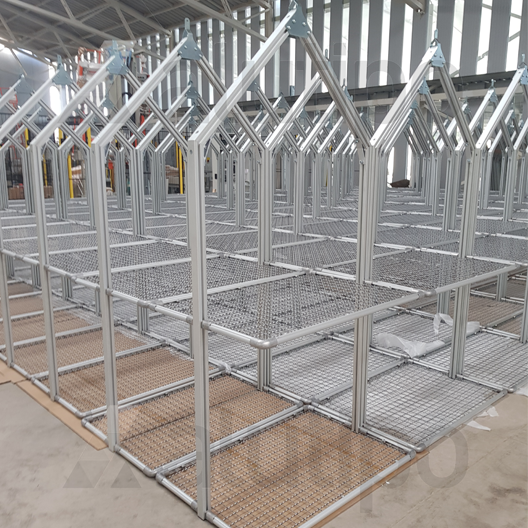

5. Modular components for easy expansion and modification.
The needs of a distribution center can change rapidly, requiring flexible and adaptable solutions. The closed-track monorail is modular, allowing for easy installation, expansion and modification. This modularity ensures that the system can grow and adapt with the business, providing a long-term solution.
6. Compact and low-profile design for versatile routing
Space optimization in distribution centers is not just about utilizing vertical space; it's also about intelligently navigating around existing structures and equipment. The compact, low-profile design of overhead conveyors allows for versatile routing options, ensuring that the system can be integrated into a variety of spaces without requiring significant modifications.
7. Easy to maintain
Maintenance is a crucial consideration for any equipment in a distribution center. Overhead conveyors are designed for ease of maintenance, with simple procedures for tensioning and lubricating the chain. This ease of maintenance ensures minimal downtime and consistent operational efficiency.
An overhead conveyor system is a cost-effective investment in operational efficiency, safety and scalability to optimize empty case handling processes. Contact us today to speak with one of our engineers!